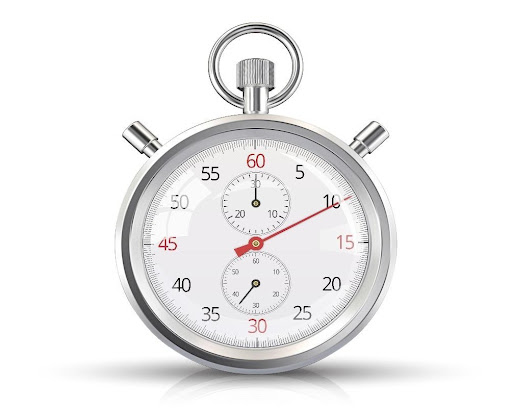
What is a Second really Worth?
Too often companies miss the hidden opportunities for efficiency gains which are prevalent
throughout every organization. I have always said… “A company’s biggest opportunity for
efficiency gains on the shop floor are at the beginning of each production shift”. An employee’s
clock in time vs the actual time a machine is producing product can sometimes vary significantly
depending on the protocol of your organization. Other obvious savings can just be a simple
analysis of operational cycle time. Weather it is machine controlled or operator dependent,
cycle time delays and automation speed rates should be analyzed in extensive detail. Here is
an example of how reducing a cycle time by just 1 second can have a dramatic effect on
efficiency.
Example: Assuming a machine has a 1-minute cycle time. The machine typically runs for 20
hours per day five days per week for 220 production days per year. Here is the calculation for
reducing the overall cycle time by just 1 second.
1 min x 60 = 60 mins
60 mins x 20 hrs. = 1200 mins/day
1200 mins/day x 220 days/yr. = 264,000 mins/yr.
264,000 mins/yr. x 60 secs = 15,840,000 secs/yr.
264,000 x mins/yr. x 59 secs = 15,576,000 secs/yr.
15,840,000 – 15,576,000/60 = 4,400 mins/60 = 73.33 hrs./yr.
1 second reduction = 3.67 days per year or 4,400 additional units produced/year.
Glenn Kennedy
Applied Manufacturing Solutions